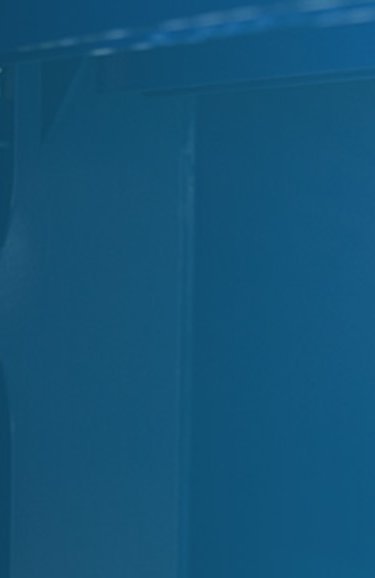
Limit dust in production areas
Due to stricter health and safety requirements as well as safety, production facilities need a way to limit dust escaping into the air from the emptying of bags in rip and tip areas.
Dust accumulation issues?
For many manufacturers, dust buildup is a regular issue.
Since health and safety requirements are becoming stricter on the amount of dust that can be present in a production environment without posing a health risk, it is crucial to have a safe and effective method to limit dust escaping into the air from the emptying of bags in those areas.
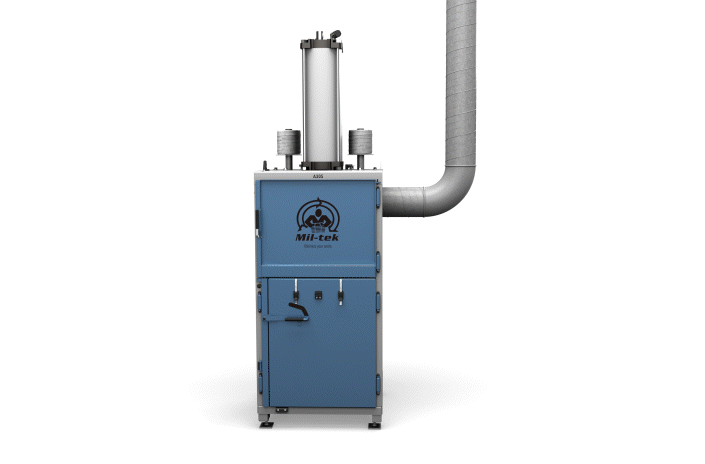
Essential steps in manufacturing create dust
For numerous industries, e.g. the food, pharmaceutical, and feed mill industries, “rip and tip” is an essential step in the manufacturing process.
Dust is naturally released into the air during the process of ripping of the outer bag, pouring of the powder items into the mixing process, and folding and disposal of the empty bag. The wish to store as many empty bags in one container before making an ineffective trip to an exterior waste container with the empty bags, adds to the dust problem.
High quantities of dust escape into the environment and elude the extraction procedure intended to remove them when these bags are further flattened in an effort to fill the waste container.

A Mil-tek solution, featuring Lean
To avoid filling containers insufficiently with empty bags, as a result of inadequate compaction, empty bags can be handled with this Mil-tek solution:
The bags can be compacted using small-footprint air-powered balers, placed directly in the production area. By compacting the bags, up to 90%, only high quantaties of empty bags are taken out of the production area and filled in containers. This results in more efficient production areas, since staff do not have to leave their station as frequently. Also, the bags are compacted inside a baler, meaning that dust also stays inside. This is all part of the overall lean compacting waste handling solution.
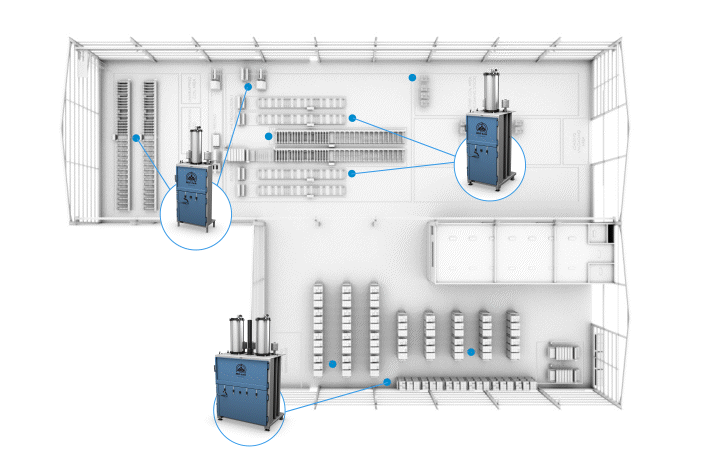
Limit dust escaping into the air
A dust extraction collar can be attached directly to the side or back of the baler. This ensures that dust is removed directly into the extraction network, with each compaction stroke, thus removing it safely and effectively from the production area.
Because there is no electricity or hydraulics in these pneumatic balers, they can be placed in high-hygiene production zones, also minimizing internal and exterior waste walks.

Have any questions about this solution?
Use this form to contact us, and we’ll get back to you right away.